
Applications
Homogeneous Granulation of Powder Systems
Typical applications where Freeze Granulation provides homogeneous granulation and drying are engineering (advanced, fine, high-performance) ceramic powders; oxides such as alumina (Al2O3), zirconia (ZrO2), silica (SiO2), nitrides such as silicon nitride (Si3N4) and carbides such as silicon carbide (SiC). Additional applications are granulation of metals and metal oxides powders, making granules for plasma spraying or catalysis, processing of nanomaterials (nanopowders), diamonds (PCD/CBN inserts), LED Lighting and graphene, graphene oxide, drying of pharmaceuticals, drugs and biomaterials like proteins, enzymes and fine chemicals.
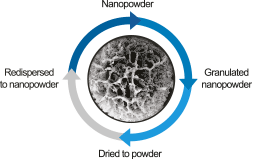
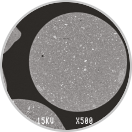
Freeze Granulation
– for improved* granule properties compared with spray drying!
(*improved granule properties: Granules with no void formation, no migration of fine particles or binders, and no formation of hard dry shell).
Please contact us for more information and a granulation test of your powder system.
Applications for Freeze Granulation
R&D-Lab powder processing
Granulation of powder mixtures in the Lab
PowderPro provides for the research and development lab equipment for Freeze Granulation, highly suitable for small scale processing of high-quality granules owing to the simplicity and easy cleaning set-up. By using the lab-scale freeze granulator, during four hours (one afternoon), it is possible to granulate 10 small batches of different compositions, including cleaning time, with high yield, without contamination and with the same granule size as achieved in large-scale granulation! In general, the mean granule size can be varied from about 20 to 500 μm with spherical shape, can easily be re-dispersed owing to the weak inter-granular bonding and be post-processed with potent performance owing to the high degree of homogeneity.
Freeze Granulation realizes “Homogeneous granulation” – homogeneous distribution of powder particles, binder or other compound mixtures for improved performance of the final products. Save time and money in lab-granulation by the quick, non-contamination and easy to clean ability, and last but not least, with excellent granule properties!
Freeze Granulation improves the granule properties vs conventional granulation methods such as spray drying producing granules with no void formation, no migration of fine particles or binders and no formation of hard dry shell.
For the spray-freezing step in liquid nitrogen we use air atomization nozzle. The normal granule size distribution is between 10-700 μm, which can be adjusted to finer, below for ex 400 μm.
In order to get fine granules we need higher air pressure resulting in higher loss of material blowing out of freezing chamber. The way to get more narrow sizes is by sieving after drying. Normally after going through this process, we get out about 90% of the input as granules, but there will be a need to include the entire size range.
Further, you can send dry powder mixes and we prepare suspensions, but we just need to agree upon necessary additives, basically dispersant and binder. Materials is to be sent to the visiting/lab address.
Please contact us and we will further discuss the opportunities with Freeze Granulation on your powder system and read more on technology and we propose a Granulation Test of your powder system.
Ceramics
Granulation of powders for Ceramics
Freeze Granulation is today used in manufacturing of various kinds of ceramics products based on functional as well as structural ceramic materials, as monoliths or composites. Typical examples are bioceramics such as zirconia toughened alumina, engineering ceramics based on high-performance powders; oxides such as alumina (Al2O3), zirconia (ZrO2) and silica (SiO2), nitrides such as silicon nitride (Si3N4) and carbides such as silicon carbide (SiC). Basically, all types of ceramic materials can be processed by Freeze Granulation, especially when homogeneous granules, easily crashed at pressing owing to the weak interparticle bonding, are requested for best possible material performance. Besides granules for pressing, Freeze Granulation can also be used as a pre-step prior to preparation of injection molding or extrusion pastes.
By effectively deagglomerate the ceramic powder in a liquid (water or organic solvent) and freeze granulate, the achieved granules can then easily be dispersed into the polymeric substance used in these shaping processes, most often in a higher powder concentration.
Additive manufacturing (Stereolithography)
- Suspension preparation by ball milling in organic media with dispersant compatible with the photopolymer system
- Freeze granulation – Easy and rapid re-dispersing into the photopolymeric resin with mild impeller stirring
- Larger batch of prepared powder can be produced and stored to be available
Metal powders
Granulation of Metal Powders in Water
Freeze granulation can with advantage be used for granulation of various kinds of metal powders for the achievement of granules with homogenous distribution of metal particles and binder or pressing aid. However, large metal particles require normally an adaptation of the liquid medium in terms of viscosity to avoid critical settling during processing.
A specific advantage with freeze granulation regarding metals is that water in many cases can be used as the freeze drying ensures very limited oxidation versus conventional spray drying in air as no liquid water/air interface where oxidation take place is present.
There is no problem to process hard metal powders (WC/Co/Cu) in water with binder (PVA, PEG, PVP) with Freeze Granulation. Diamonds can be mixed in a slurry, but with larger sizes (>100 um) problems with segregation due to difference in density will increase.
As we use air atomization in Freeze Granulation, the size distribution of granules will be approximately 10-700 um, but can be adjusted by spray settings to the finer or coarser side.
We cannot guarantee one diamond in each granule since granule sizes vary. The results produced will not all be consistent, but for the pressed green body, which is a type of granule, the distribution of diamonds will be homogeneous.
For solvents we use Cyclo-hexane or Tert-Amyl alcohol. Ethanol and Acetone have too low melting point for FG. We only use organic solvents when powders actually react with water. Most metal powders can be processed in water. There is very limited oxidation since drying is made under vacuum. Paraffin wax can be used in Cyclo-hexane, but processing in water systems is always preferred. Dryer needs to be tray type with heated shelves.
PIM-formulation
Freeze Granulation offers a technique where a powders suspension is atomized, the droplets are instantly frozen and subsequently freeze dried resulting in highly homogeneous granules. This technique can with advantage be used for pre-preparation of fine powders prior to mix it into a PIM-formulation. Colloidal processing by ball milling in water or a solvent to properly deagglomerate the powder prior to Freeze Granulation ends up in homogeneous granules with weak interparticle bonds. Hence, the powder can easily be re-dispersed into primary particles within the PIM-formulation with preserved homogeneity, without heavy mechanical treatment, and, often to a higher powder loading than possible with direct mixing. Other compounds intended to be used in the PIM-formulation can also be added prior to Freeze Granulation for an effective formulation mixing. PowderPro AB provides equipment for Freeze Granulation as well as know-how of powder suspension processing.
Please contact us for more information and a test-granulation of your powder system.
Diamond tools
Diamond tools and grinding wheels
Freeze Granulation is today used by market leaders in manufacturing of Diamond Tools; cutting and polishing wheels, drill bits for rock tooling and other applications. Our technology is also being used in manufacturing of PCD – Polycrystalline Diamonds. Homogeneous distribution of the active component, diamond particles, in the wheels is crucial for the cutting performance and tool life.
By using Freeze Granulation you will transfer your slurry including diamonds, fillers and binders into granules with homogeneously distributed diamond particles. The superb homogeneity results in improved cutting performance and tool life of the pressed and sintered advanced diamond composite product. By adding diamonds prior to granulation, the risk of agglomerated diamonds is minimized in comparison to when they are added after a granulation or dry mixed.
Please contact us and we will further discuss the opportunities with Freeze Granulation on your powder system and read more on technology and we propose a Granulation Test of your powder system.
Thermal spraying
High-quality granules for thermal spraying
Freeze granulation is today being used to produce high-quality granules. This technology enables the use of fine, submicron metallic or ceramic powders, shaped into homogeneous spherical granules with excellent flow properties, highly suitable for thermal spraying processes. The use of fine powders gives possibilities to produce coatings with higher material performance compared to what is normally achieved with conventional powders.
Please contact us for more information and a test-granulation of your powder system.
Material synthesis
Material Synthesis using Freeze Granulation
Freeze granulation is an excellent tool for precursor preparation in material synthesis. Soluble or non-soluble compounds are initially mixed in water or a suitable organic solvent, optionally by mechanical treatment such as ball milling. The homogeneous solution/suspension is then freeze granulated with preserved homogeneity in the dried granules ensuring a high yield of desired material composition after the subsequent thermal treatment (calcination). The only restriction regarding solvent and precursor composition is that the resulting freezing point of the solution/suspension cannot be lower than about -20°C to avoid melting during the freeze drying operation. As freeze granulation provides granules with comparably low density, it will also be easier to disintegrate the calcined material into the desired size compared to what can be expected when conventional drying of the precursor mix has been used in the preparation step.
Please contact us for more information and a test-granulation of your powder system.
Material research and development
Freeze Granulation in material research and development
Besides its use for making high quality powder granules for pressing, freeze granulation can, with advantage, be used for many different purposes in material research and development. The homogeneity preservation, weak bonding within the granules, limited oxidation of sensible materials, limited damage of organic compounds and, not at least, the possibility to conveniently process numerous small batches of material makes the use of this technique manifold. Preparation for material synthesis, preparation of easy re-dispersible nano powder or CNT (Carbon Nano Tubes), production of carrier particles for catalysts or other purposes are only a few examples of the utilization. As you get familiar with the process and its capacity, only your imagination is the limit.
Freeze granulation can also be used as a pre-preparation step of fine ceramic powders where it is properly dispersed in a low viscous medium (water or organic solvent) with a dispersant compatible with the MIM system. After freeze drying, the result will be a powder very easy to be dispersed into the MIM system (wax or polymer melt), supporting high powder concentration and homogeneity.
Please contact us for more information and a test-granulation of your powder system.
Graphene
Freeze Granulation of Graphene
Freeze granulation gives the possibility to granulate nanpowders, like graphene platelets or graphene oxide, achieving granules with high degree of homogeneity which are easily redispersed (if applicable) in a liquid or disintegrated at a pressing operation. This is owing to the soft drying process giving week inter-particle bonding compare to what is obtained in conventional drying. Consequently, the nanosized material properties will be preserved, i.e. nano will still be nano. You can re-disperse agglomerated graphene oxide powders back to dispersed graphene particles in water or in organic solvents. Freeze drying of granules also prevents oxidation of metals or non-oxide materials as conventional drying does not, especially critical for graphene and graphene oxide.
Wet granulation of graphene platelets
Freeze Granulation of graphene platelets is being used for to make homogeneous mixtures of dry granules with graphene or graphene oxide. When applying FG on a Graphene slurry, you will keep the homogeneous dispersion of the nano/macro Graphene particles/platelets in the FG-granules and you can easily re-disperse the granules to nanoparticles by stirring. In the next step you can homogeneously mix graphene granules with other polymers or premix Graphene and polymers and then FG to a homogeneous granules.
For ex, see article on properties of SiC composites with GNPs, GO and in-situ formed graphene.
Please contact us for more information and a test-granulation of your graphene powder system.
Nanoparticles
Freeze Granulation of nanoparticles and nanopowders
Freeze granulation gives the possibility to granulate nanpowders, like graphene platelets and graphene oxide, achieving granules with high degree of homogeneity which are easily redispersed (if applicable) in a liquid or disintegrated at a pressing operation. This is owing to the soft drying process giving week inter-particle bonding compare to what is obtained in conventional drying. Consequently, the nanosized material properties will be preserved, i.e. nano will still be nano. Freeze drying of granules also prevents oxidation of metals or non-oxide materials as conventional drying does not, especially critical for nanoparticles.
Nanopowders can be granulated and dried into a powder and then redispersed to nanoparticles again avoiding agglomeration (aggregates), which is not possible with other granulation methods like spray drying. By Freeze Granulation of nanomaterials you can easily redisperse the dried powder to the primary particles only by simple impeller stirring in water, see illustration below.
Please contact us for more information and a test-granulation of your powder system.
LED-lighting
Homogeneous granulation of doped phosphor LED Lighting
Freeze Granulation provides today homogeneous granules for commercial production of ceramic phosphor plates for white illumination in LED Lighting. By using Freeze Granulation of the powder/binder mixture, compared with spray drying, it is possible to manufacture homogeneous phosphor plates with superior properties for generating soft and warm white light from high power LEDs versus what can be achieved with conventional spray drying.
Studies of photoluminescence in LED Lighting have shown that nano-scale YAG phosphor powders emit a higher intensity of luminescence than that provided by sub-micro sized samples. By using Freeze Granulation, nanoparticles will be kept nano-sized in the sintered product. Therefore, it is expected that freeze granulation can support glass-ceramic phosphor as a promising candidate for the realization of resin-free, high-temperature and high-humidity resistant and long-time durable white LED devices.
Cryogenics
Cryogenics – Processing of Materials
Freeze granulation is a commercial method for cryogenic processing (granulation) of chemicals and powder-based materials. A unique cryofixation of the material in small droplets gives homogeneous granules and improved properties in the final product.
The slurry is pumped and sprayed into liquid nitrogen for instant freezing of the derived droplets. The frozen droplets (granules) are then freeze dried in a freeze dryer to remove the solvent (water or organic solvent) by sublimation with a minimum damage of organic compounds and without disturbing the homogeneity.
Pharmaceutical and biomaterial drying
Pharmaceuticals and drugs (Pharma industry)
Freeze Granulation (FG) or Spray freeze drying (SFD) is being used for drying of pharmaceuticals and drugs, and for drying of biomaterials like proteins, enzymes and fine chemicals. The low-temperature and soft freeze drying is an important advantage to minimize damage of organic compounds and improve solubility (re-disperse) for optimized bio effect. In addition, applications in apparent solubility enhancement, pulmonary drug delivery, intradermal ballistic administration and delivery of vaccines to the nasal mucosa.
FG or SFD is a comparatively new method to produce biopharmaceutical powder preparations. This method combines spray of the feed liquid and freeze-drying (FD) processes to obtain a fine powder preparation. SFD requires less time than the FD process due to high heat transfer. Spray freeze drying in a fluidized bed at normal and low pressure. SFD powder has a large specific surface area and a higher fine particle fraction than those of FD powder.
For SFD powder, droplets formed by spraying the solution are immersed in liquid nitrogen. FD products can be reconstituted more quickly and easily as the process forms microscopic pores. The drying of frozen particles in trays and in vials on trays. Thermal treatment, annealing could be added before FD. The annealing process alters the microstructure of a material causing changes in properties. In general, the annealing treatment confers a certain homogenization to the ice crystal size distribution. The SFD method has a lot of advantages including good aerosol properties, small particle size control, and high yield. Additionally, the particle densities of SFD powders are significantly reduced compared with that of raw powder. According to the definition of aerodynamic particle diameter, the SFD process provides powder with an aerodynamic particle size suitable for inhalation.
Protein aerosol powders
Freeze granulation, in contrast to spray drying, has been shown to produce protein particles with light and porous characteristics, creating powders with superior aerosol performance due to favorable aerodynamic properties. This promotes the freeze granulation technology suitable for making protein inhalation powders.
We suggested applying Freeze Granulation for to make unique powder in the pharmaceutical industry. Heat-sensitive pharmaceuticals such as insulin and anodyne are applicable to the FG process and will be easy and quick to re-dissolve.
Please contact us for more information and a test-granulation of your powder system.