
Technology
The history of Freeze Granulation
In mid 70th W.W. Rhodes and S. Prochazka (1975) provided the first publications about the technology Freeze Granulation of ceramic powders without defining the advantage or explaining the positive results.
Freeze granulation, spray freezing and subsequent freeze drying (lyophilization or cryodesiccation), a development of Spray Freeze Drying (SFD) and Spray Freezing into Liquid (SFL), was first developed for granulation of ceramic powders at Swedish Ceramic Institute (SCI) in Göteborg in the late 1980’s. It was early shown to be the most suitable method to provide optimal granule properties for lab and research purposes and, later on, also for pilot and production scale processing of ceramics and other powder-based materials.
The unique benefit with the Freeze Granulation technology is to make “homogeneous granules of mixed nano/micron powders with binders”.
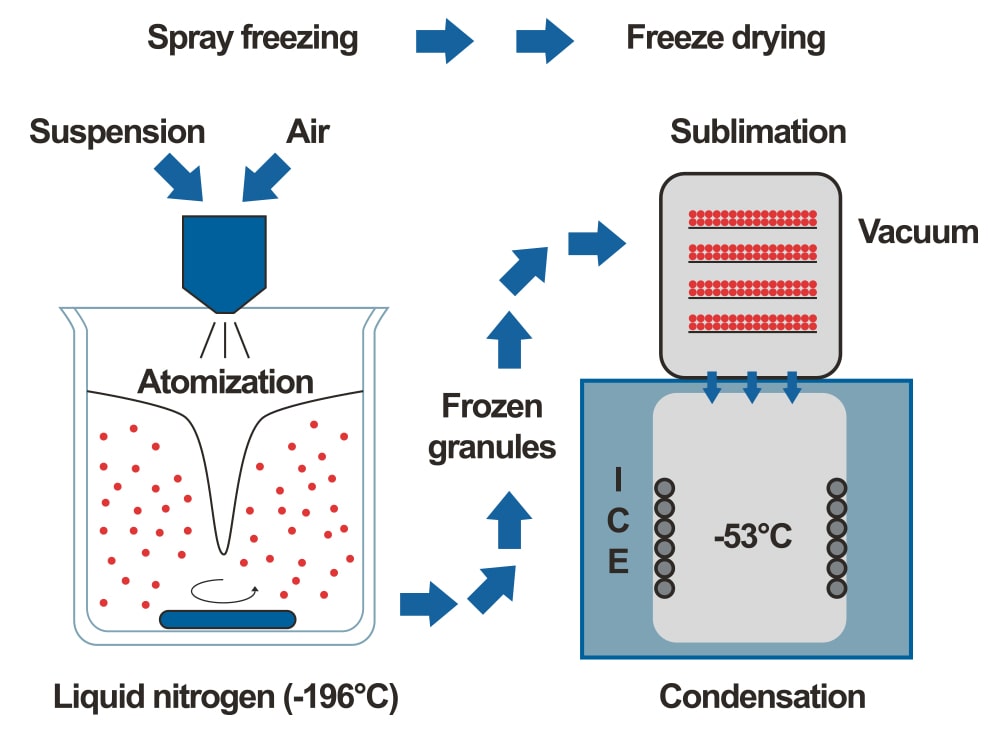
During the 1990’s, Freeze Granulation was successfully applied in material and processing developments within many research projects and commercial contract work. Specific powder systems from various companies were tested with very good results, demonstrated by homogeneous granulates and improved final component/material properties. However, no commercial equipment was available and therefore PowderPro AB was founded in January 2000 with the objective to provide wet granulation equipment for the Freeze Granulation process.
PowderPro AB develops, manufacture, market and sell granulation equipment and carries out test granulations (standard concept), whereas RISE IVF handles the developments with regards to suspension concepts and granulation methodology.
Please contact us for more information and a test-granulation of your powder system.
PowderPro AB
Several companies and research labs around the world have applied the Freeze Granulation process with the support of PowderPro AB. Typical applications for freeze granulation are homogeneous granulation and drying of ceramic powders; oxides (Al2O3, ZrO2, SiO2), nitrides (Si3N4) and carbides (SiC) and also metal oxides, nanomaterials (nanopowders), diamonds, LED Lighting, igniters, delay elements and pharmaceuticals like proteins, enzymes and chemicals.
Freeze Granulation yields free-flowing, dust-free and easy to dose granulates – The way to optimal powder processing!
PowderPro offers wet granulation equipment ex LS-2 for Freeze Granulation of powders to granules.